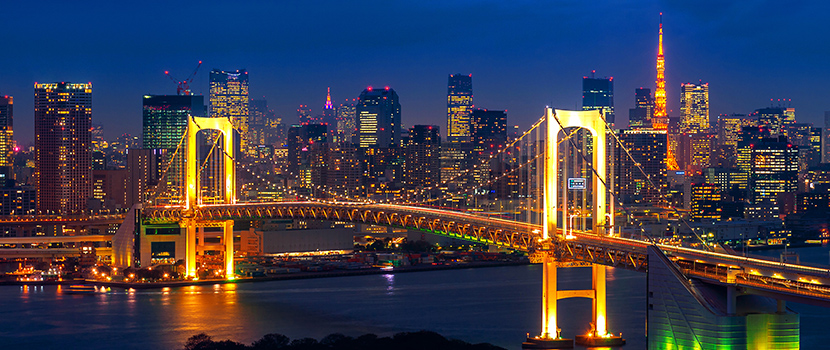
Examples for power generation field
Kleentek's proposal to those involved in power generation
What problems are you having?
Hydraulic oil control for power generation
① Issues for hydraulic oils
Hydraulic oils used for operating a speed governor and inlet valve are not fed directly into pump to move cylinder but first sent to a pressurized oil tank and the oil will be kept at constant pressure. The oil which was kept at constant pressure is used as source of pressure to move cylinder.
When oil is pressurized by air, a large amount of air is dissolved into oil following the Henry’s law. The dissolved air will be bubbled out when the oil returns to an oil tank in atmospheric pressure.
② About malfunctions of hydraulic valves.
Occasionally black lines and/or dark brown or brownish red sticky substances is observed along the walls near the surface of the hydraulic oil tank. They are carbons and oxidation products. They are generated because when air bubbles trapped in oil are subjected to adiabatic compression, they get heated to generate carbons through shearing of oil molecules or oil oxidation products. Filters cannot remove these oil oxidation products, resulting in malfunction of valves. With the electrostatic cleaner, EOC, such carbons and oil oxidation products can be eliminated.
③ Issues on lubricating thrust bearings.
Thrust bearings support the giant rotating water wheel at a hydropower plant. These bearings are known to be protected by about 50 micrometer thick fluid lubricant films. If foreign materials and/or water penetrate this lubricant film, lubrication is disrupted.
④ Thrust bearing lubricant oil control
Since a water wheel rotates by water pressure, there is a possibility of water getting into the lubricant oil. Water not only initiates rusting or oxidizing oil, but also is a very poor lubricant. Top priority of thrust lubricant control is to eliminate water content and the contaminants that induce wear once migrated in the lubricant film.
For removing water content, a dehydrating filter DH ,is effective. DH filter element is a deep layer filter with about 50 micrometer porosity for filtering – since pumping rate is set low, the water removal proceeds in a stable condition. After absorbing water, this fiber expands making the filter mesh smaller so that the contaminants less than 50 micrometer may be also removed. Because of low pumping rate, there is no electrostatic charge induced by oil to filter friction. In addition, the filter element wet with water would not retain electrostatic charges. EDH is the best unit for oil control, combining dehydrating filter DH with electrostatic cleaner.