Technology
Oil purification
“Oil purification” means removing contaminants from oil to make it clean, and there are various standards for judging “cleanliness”.
Commonly used standards include NAS1638 (NAS cleanliness coding) and ISO4406 (ISO cleanliness coding), which measure the size and number of contaminants in oil and assign a cleanliness code. Another evaluation method is the mass method. This is a method of evaluating the weight of contaminants contained in a specified amount of fluid as the “contamination degree” rather than the size or number.
Each has advantages and disadvantages, but NAS and ISO cleanliness coding have a trap when it comes to managing hydraulic fluids.
For example, in the case of NAS cleanliness coding, contamination of 5 μm or less will not be measured or evaluated.
Even if there is a large amount of contaminants of less than 5 μm in the oil, if there is little contaminant of 5 μm or more, it will be evaluated as a clean oil according to the NAS cleanliness coding. (in the case of ISO cleanliness coding, the minimum evaluation area is 4μm© or more)
Various types of contaminants exist in oil, many of which are less than 5 μm.
As an example, please look at the contamination distribution below.
Contamination distribution
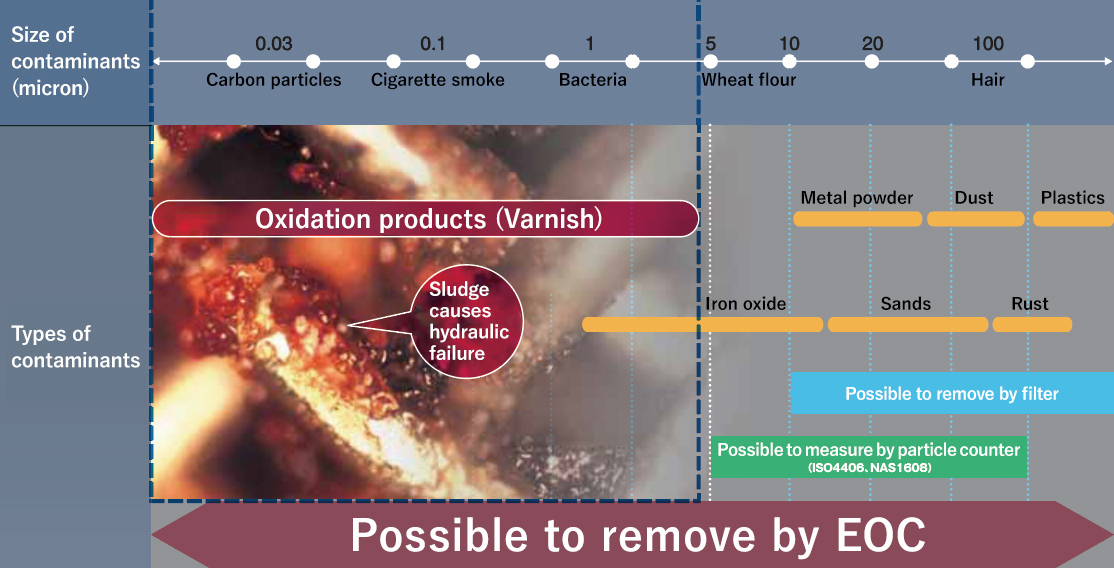
The above table shows the contaminations in hydraulic oil used for a long period of time by size and type. When hydraulic oil is used for a long period of time, there will be many contaminants of 5 μm or less in the oil, and in the range of 1 μm or less, oil derivation contaminants “oxidation products, varnish” will become the main contaminants.
These oil oxidation products are precipitated in the oil as oxides when the oil combines with oxygen, but because they are very fine particles, they are difficult to capture with a conventional filter. In fact, there is a limit to the size of contaminants that can be captured by oil management using a filter, therefore oxidation products remain in the oil and their concentration increases over time.
Oxidation products tend to adhere to metal surfaces, so tank walls and inside of pipes are contaminated with oxidation products.
Eventually precision hydraulic parts such as valves are severely affected in such an environment.
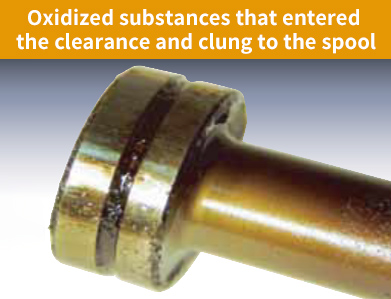
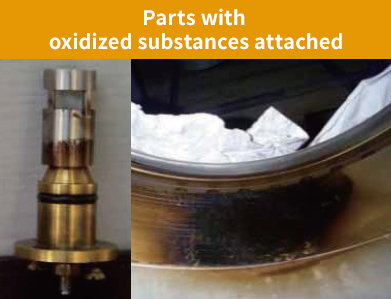
A Varnish Removal Solution For Your Entire System Ensuring Optimal System Performance
Varnish Deteriorates System Performance
The varnish in oil acts as a catalyst to shorten the life of oil. In addition, the nature of varnish attracts other contaminants in oil, converting smooth metal surface to sandpaper.
A product of oil oxidation, varnish coats the surfaces of servo and proportional valves and pump impellers, resulting in increased friction. Unfortunately, the change in friction in these highly sensitive and close tolerance components can cause unwanted effects,
Including:
– Reduced machine performance
– Constant valve adjustment
– Loss of control stability
– Erratic cycle times
– Increased downtime
Solving Vanish Problem
Unlike tradition oil filter, the KLEENTEK electrostatic oil cleaning method removes oil contaminants to sub-micron levels, maintaining the oil and your oil system in optimum condition for trouble-free production
How It Works
KLEENTEK electrostatic oil cleaner (EOC) are dedicated oil purification and varnish removal system designed for installation on hydraulic and lubrication equipment. Through a kidney-loop process, the EOC draws oil from a main oil reservoir and circulate it a low velocity.
The EOC does not charge particles or the oil, but instead, use a vertically positioned electrode to produce a high potential electrostatic field between itself and a ground surface within the pleated cellulose collector element. As oil passes upward through this patented collector element and parallel to the electrode and ground surfaces, suspended contaminants in oil as small as sub-micron are forced by the voltage field against the collector media and removed from the oil. As oil flows freely through the EOC, the contaminants suspended in oil, sub-micron particles, dust and oil oxidation products, including the varnish are removed.
KLEENTEK electrostatic oil cleaner use the principles of electrostatic for particle and varnish removal, as well as oil purification via electrophoresis (removal of naturally charged particles by electrostatic force) and dielectrophoresis (removal of a charge-neutral particle by gradient voltage field force). A particle with a positive charge is drawn toward a negative electrode in a cleaning chamber, while one with an inherent negative charge is drawn toward a grounded pleat. A charge-neutral particle will move towards stronger part of the deformed electric field generated by pleated type collector.