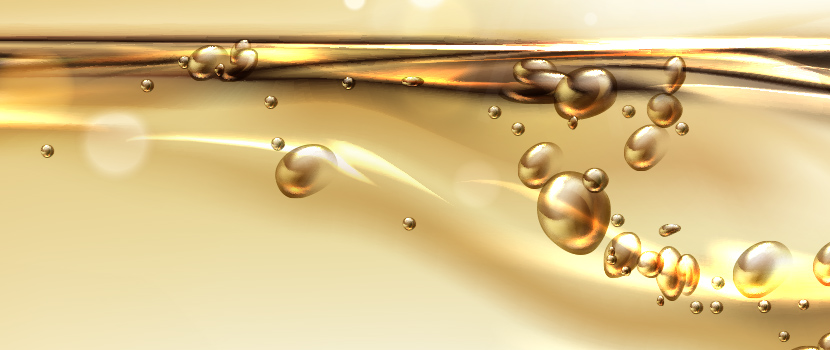
Power savings/Prolonged oil life
Realization of power savings
reduced electricity cost via electrostatic oil cleaner
We would like to report successful management of hydraulic oil using electrostatic oil cleaner, enabling to save electric consumption of machines.
When an electrostatic oil cleaner is used to clean oil, power consumption is significantly reduced resulting in cost cuts – even taking into account the electric cost for running the electrostatic oil cleaner.
Measurement method | Attaching a power meter and a printer to the 850 ton molding machine of Company T, we measured its average power usage every 30 minutes one week before oil cleaning was performed. We did the same 9 days after oil cleaning was performed. |
---|---|
Conditions of the molding machine | ・Oil quantity: 2900L (liter) ・Oil name: Super Highland 46 ・Oil temperature: 42℃ ・Filter used: Strainer and bypass filter (line and return filters not used) ・Motor: 3 units. |
Service period of oil | 7 years and 9 months (with some replenishing only) |
Oil cleaner deployed | EOC-100 |
Grade of oil contamination | before cleaning: 0.7mg/100ml, off the NAS grade; after cleaning: 0.5mg/100ml NAS Class 7 |
Measurement results | Average power / Before cleaning:18.0kw After cleaning:16.5kw Power saving:1.5kw Power saving:8.3% |
Electricity cost saving | ・Operating times 24hrs x 20days/mo x12mo/yr ・Unit cost of electricity: 10.2 JPY/KWH Actual electricity saving is obtained by subtracting power consumption of electrostatic cleaner. Power consumption of installed electrostatic cleaner, EOC-R25: 0.2kw ・Annual power saving (for 3 motors serviced by one unit) =(1.5(kw) x 3-0.2(kw)) x 24(hrs/day) x 20(days/mo) x 12(mos/yr) x 10.2(JPY/kw) =252,633JPY/unit Since there are 27 molding machines in operation at the plant, total power saving per plant is 27 unit x 252,633JPY=6,821,091JPY |
Prolonged oil life
Table below shows the changes in oil conditions for 7 years when the electrostatic oil cleaner is used. As apparent in this table, the cleanliness, the NAS class, and water concentrations are all controlled to normal conditions, requiring no need of oil replacement for 7 years in order to make malfunction-free operation of machines.
Changes of oil conditions for 7 years after installing the electrostatic dust cleaner.
Machines used | Hydraulic simulator (equipped with 6 servo valves) |
---|---|
Oil quantity | 6000L |
Oil name | Mulpus 32 |
electrostatic dust cleaner | EOC-50 |
Equipment 1
Years of service of oil | 1st year | 2nd year | 3rd year | 4th year | 5th year | 6th year | 7th year |
Cleanliness (mg/100ml) | 0.3 | 0.2 | 0.3 | 0.3 | 0.4 | 0.4 | 0.3 |
NAS Class | 4 | 5 | 6 | 6 | 5 | 4 | 6 |
Water content (PPM) | 80 | 30 | 80 | 50 | 80 | 40 | 50 |
Equipment 2
Years of service of oil | 1st year | 2nd year | 3rd year | 4th year | 5th year | 6th year | 7th year |
Cleanliness (mg/100ml) | 0.3 | 0.3 | 0.3 | 0.3 | 0.4 | 0.4 | 0.2 |
NAS Class | 5 | 4 | 6 | 6 | 4 | 5 | 7 |
Water content (PPM) | 90 | 30 | 80 | 50 | 80 | 20 | 30 |
Equipment 3
Years of service of oil | 1st year | 2nd year | 3rd year | 4th year | 5th year | 6th year | 7th year |
Cleanliness (mg/100ml) | 0.3 | 0.3 | 0.2 | 0.2 | 0.4 | 0.2 | 0.2 |
NAS Class | 5 | 5 | 6 | 6 | 3 | 5 | 7 |
Water content (PPM) | 80 | 30 | 80 | 50 | 70 | 30 | 40 |
1. Cleanliness: maintained for 7 years at 0.2mg/100ml – 0.4mg/100ml of cleanliness level.
2. NAS Class: controlled to NAS Class 3-7.
3. Water content: controlled to 20ppm-90ppm
4. Oil replacement: None for 7 years (vs. once a year replacement before installing the electrostatic cleaner)
5. Hydraulic malfunctions: none for 7 years including servo valves
6. Collector exchanges cycle: every 2000 – 3000 hours